BBN supply din en 10149-2 weldability
Our quality control department will do inspection for details of the steel materials din en 10149-2 before delivery. We would invite the customer side to attend the inspection together. If they can not come, we will also take rich pictures for them to che
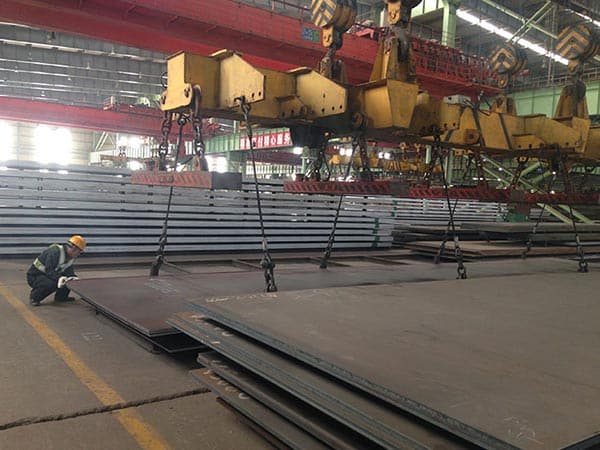
Our quality control department will do inspection for details of the steel materials din EN 10149-2 before delivery. We would invite the customer side to attend the inspection together. If they can not come, we will also take rich pictures for them to check. Meanwhile, we will publish inspection report and send them the PDF version. Besides, we accept any third party inspection such as SGS, BV, etc. And our quality control department will support the third party to inspect the steel materials smoothly and try our best to deliver the qualified steel materials to customers earlier.
The din en 10149-2, wear-resistant steel plate has good impact properties:The wear-resistant steel plate has a double-layer metal structure. The wear-resistant layer and the base material are metallurgically bonded. It has high bonding strength and can absorb energy in the process of impact. The wear-resistant layer will not fall off. The wear-resistant steel plate can be applied to the working conditions with strong vibration and impact, which is better than cast wear-resistant materials and ceramic materials.
Using advanced logistics management, advanced models and management experience to increase the reliability of logistics operations and provide customers with 24/7 cargo management. On the premise of reducing transportation and management costs as much as possible, we provide customers with high-quality and efficient services; good business reputation has been recognized and supported by our customers.
In the second step of hot rolling process, different finished mills are used to roll billets or continuous casting billets into finished steel of proper shape and size. This din en 10149-2 production process is called finished product production, which is generally divided into two stages of rough rolling and finish rolling. In the roughing stage, a large amount of reduction (reduction per pass) is adopted to reduce the number of passes and improve the output; after roughing, the finishing stage is entered, and the finishing is carried out with a small amount of reduction to achieve a good surface and accurate din en 10149-2 size.
Leave a message