What is the difference between alloy steel and s550mc high strength steel auto plate
It is very important for an enterprise to have a sound after-sales service system, which not only ensures the normal outflow and inflow of the company's products, but also improves the trust of the company's products in the hearts of customers.
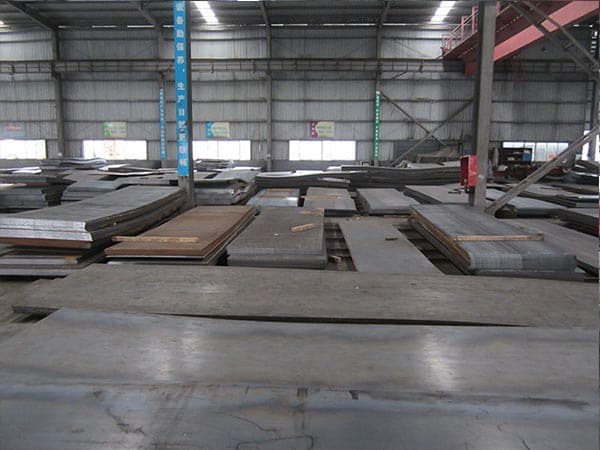
It is very important for an enterprise to have a sound after-sales service system, which not only ensures the normal outflow and inflow of the company's products, but also improves the trust of the company's products in the hearts of customers. Our company has a special after-sales service team and good after-sales service reputation. In case of any problem in the use of our steel products S550MC high strength steel auto plate , whether quality problem or not, the after-sales service department will assist in solving the problem as soon as possible, and regularly consult and track the use of the steel products.
In the face of domestic and foreign steel situation, based on the advantages of production and inventory, we have established our own processing center, and our manufacturing includes different types. Steel s550mc high strength steel auto plate surface treatment - such as steel pretreatment (shot peening and shop primer), steel galvanizing; steel structure processing - such as cutting, drilling, milling, turning, bending, welding, etc.
The quality grade of common carbon structural steel Q235 can be divided into A, B, C, D and E. Relatively, the quality of Q235A is poor and that of Q235E is the highest. Different grades of Q235 steel have different characteristics, which are mainly different from the impact temperature: Q235A does not require impact toughness test; grade Q235B is for room temperature (20℃); grade Q235C is for 0℃; grade Q235D is for - 20℃; grade Q235E is for - 40℃. The s550mc high strength steel auto plate, carbon structural steel Q235 has good combination of strength, plasticity and welding properties.
The after-sales service department will pay return visit to each customer by call or email, report problems found during the return visit in time, and discuss with the production and quality inspection center to propose effective solutions and follow up in a timely manner, so as to ensure the benefits each customer are fully guaranteed, and to provide customers with more value-added services.
Leave a message